Project Portfolio
Here are just a few examples of robotic projects completed in the recent past. Call us about more examples or to discuss your specific application.3D and 2D Vision Robotic Guidance - Bin Picking and Part Loading
Challenge: Expensive structured racks were used to present parts to be loaded into Machining Centers. Customers were looking for a way to replace these low part capacity racks with high capacity, in-expensive bins, to reduce robot collisions inside racks, streamline forklift traffic and WIP storage space, and increase productivity by 20-25%.
Midwest Robotics Solution: Midwest Robotics engineering has 20 years of experience working with robotic vision systems. We started with improving robot calibration-mastering to achieve required positional accuracy of FANUC robots for this machine vision guided application. Our engineers designed a prototype cell featuring 3D Vision System (FANUC 3DAS), iRVision-2D vision aligning station, rugged EOAT, ability to do bin-picking of up to 32 part models without a tool-change or vision process change. Lead users quickly confirmed that the pilot system met KPI metrics. Customers ordered additional 11 systems from Midwest Robotics.
Bottom line: Midwest Robotics solution allowed our customers to reduce operating costs by $125-150K/quarter, cut WIP storage space 2.5 times, and improve productivity by 25%. This was the first success of applying 3D vision and bin-picking technology in mass production in the USA.
Vision guided palletizing and de-palletizing
Challenge: An automated case handling system that is able to locate a pair of cases in each layer, on up to 7 layers deep pallet. Pallets with cases are roughly located, however a high accuracy of case placing on a conveying system is required.
Our Solution: For this project, we applied a robot mounted 2-D vision system to accurately located and de-palletize 3-D stacks of cases, up to 7 layers deep, compensating up to +/- 4 inches and 30 deg of displacement. Solution included a FANUC M410iB palletizing robot, FANUC vision system, vision lighting, application setup and programming.
Bottom line: Elimination of hard automation - mechanical aligners and guides, by using a flexible, higher productivity vision guided robot system.
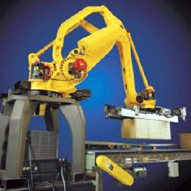
Deflashing of automotive fuel tanks and other plastic parts
Challenge: Hand trimming of plastics is not safe and labor intensive. Part shrinkage is difficult to compensate. Automated trim fixtures and other trim robots do not compensate for part shrinkage. Other vision or sensor based algorithms are complex and not cost effective to implement.
Our Solution: We have worked with robotic deflashing of plastic since 1998. Based on years of experience we developed a real world deflashing solution. Our deflashing solution feature a FANUC robot equipped with Accudeflash(TM) EOAT (USPT 6,086,294). On top of that, we package a robot with our uptime oriented tools and software to make it real production ready. The high performance cutter stays on the parting line regardless of shrinkage. Our customers wittnessed cutter life of 67 linear miles on HDPE. Also works on LDPE, TPO, Polycarbonate, and other plastics.
Bottom line: Up to Class A trim quality. Deflashing Robot keeps up with a mold. Over 60 successful AccuDeflash(TM) systems in US and Europe.
Glass Sealing and Dispensing Robotic Systems
Challenge: How to ensure uniform sealant application along complex part shapes, such as automotive glass, body panels or reinforcements? It is difficult for an operator or a conventional mechanism to dispense sealant with a consistent profile. For robotic systems, this is also difficult to teach a new dispensing path in a short time frame, regardless if a robot is holding a part or a tool.
Our Solution: We have developed turn-key sealing systems using our know-how of FANUC or Motoman robot technologies. Our sealing solutions use an intelligent, closed-loop control system to monitor robot's actual TCP speed and adjust flow of sealant with high degree of control cold or (pre) heated sealant delivery.
Bottom line: Our clients realize greater value of our robotic sealing solutions: 1) setup of new part models in a shorter time for (fixed or robot mounted) sealing tooling; 2) increase in productivity; 3) increase in part yield by 5-20% due to consistent and accurate application of uniform bead of sealant along straight lines, curves or sharp corners.
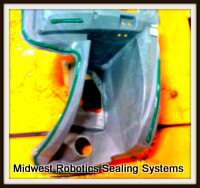
Vision guided part loading
Challenge: Identify party orientation (+/- 180 deg), locate and pick automotive parts (e.g. castings, or automotive backlites / sidelites), and load them repeatedly into process equipment (such as a machining center or a tempering furnace). System should be flexible to handle up to 100 different part styles and part loading accuracy of less 1mm. Robot inaccuracy, gripper inaccuracy and vision calibration inaccuracy stack up total error for such system.
Our Solution: We applied FANUC R2000i-165F robots, FANUC 2DV vision systems, along with our vision calibration and robot setup know-how. Midwest Robotics designed and setup lighting, optics and vision software. We applied special calibration techniques to improve accuracy of loading large and small customer parts to ensure robot can load with higher accuracy.
Bottom line: Exceeding customer expectations of high accuracy (less 0.5mm), flexibility, low cost, and ease of use of the system. Over 75% of robots we integrate involve vision technologies. In addition to new systems, we help clients to improve their existing vision systems, which were built by somebody else but are not performing to client's expectations.
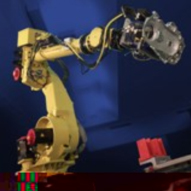